Magnetic Materials

MAGNETIC MATERIALS
To understand magnetism, it is essential to identify what types of materials are used to create magnets and how the materials used affect the ultimate performance of a magnet.
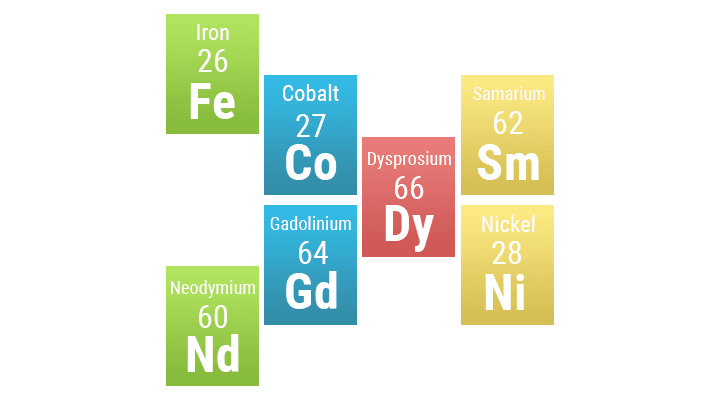
Introduction
There are a number of elements that are attracted by magnets, commonly referred to as ‘magnetic’. These are the same materials that can be magnetised to create permanent magnets, Here you can see a list of magnetic elements and minerals:
Magnetic materials are categorised as magnetically hard, or magnetically soft materials. Magnetically soft materials are easily magnetised but the induced magnetism is usually temporary. For example, if you rub a permanent magnet along a nail or a screwdriver, the nail or screwdriver will become temporarily magnetised and will emit its own weak magnetic field. This is because a large number of their iron atoms are temporarily aligned in the same direction by the external magnetic field.
Like magnetically soft materials, magnetically hard materials can be magnetised by a strong external magnetic field, such as those generated by an electromagnet. The difference being that magnetically hard materials will remain magnetised indefinitely, unless they are demagnetised by an opposing magnetic field, raised above their curie temperature or allowed to corrode.
Magnetically hard materials are used to create permanent magnets made from alloys generally consisting of varying amounts of iron, aluminium, nickel, cobalt, and rare earth elements samarium, dysprosium, and neodymium.
The strongest permanent magnets are known as neodymium magnets and are made from an alloy of neodymium, iron, and boron. Permanent magnets are difficult to magnetise as unlike magnetically soft materials their atomic magnetic domains aren’t easily aligned but once they are aligned, they remain so indefinitely.
Classification of Magnetic Materials
Because all materials have a different atomic structure different materials react differently when placed in a magnetic field. In its simplest form, the magnetic behaviour of a material is determined by its number of unpaired electrons in each atom.
In the atoms of most elements electrons exist in pairs with each electron spinning in a different direction causing them to cancel out each other’s magnetic field, therefore no net magnetic field exists.
However, some materials have unpaired electrons which will generate a net magnetic field and therefore have a greater reaction to an external magnetic field. Most materials are classified either as ferromagnetic, diamagnetic or paramagnetic.
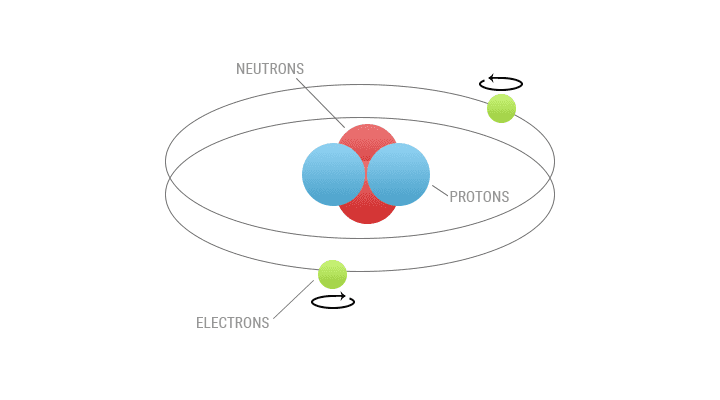

FERROMAGNETIC
Ferromagnetic materials have some unpaired electrons in their atoms and therefore generate a net magnetic field, albeit a very weak one. This is because the individual atoms or groups of atoms, known as magnetic domains, are randomly aligned cancelling each other out.
When an external magnetic field is applied to the ferromagnetic material the individual domains are forced into alignment which they maintain once the external field is removed therefore maintaining their magnetism, known as remanence. Iron, nickel and cobalt are all ferromagnetic materials.
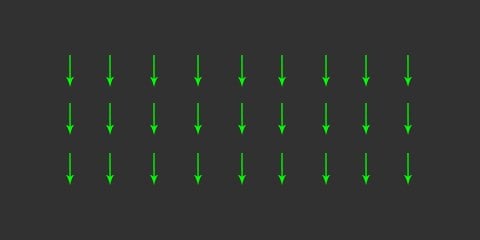
DIAMAGNETIC
Diamagnetic materials repel any externally applied magnetic field. This occurs because their magnetic domains realign to oppose an externally applied magnetic field when influenced by a magnetic field. All materials show some diamagnetic properties, however, in most materials, the effect is extremely weak and unnoticed.
All the electrons within the atoms of diamagnetic materials are paired, therefore they do not generate their own net magnetic field. Most elements in the periodic table are diamagnetic.
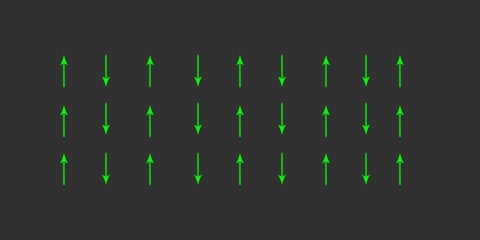
PARAMAGNETIC
Paramagnetic materials have a small susceptibility to magnetic fields meaning that they are slightly attracted by a magnetic field. However, unlike ferromagnetic materials they do not maintain their magnetic properties once the external magnetic field is removed.
Most elements are paramagnetic, however, because their attractive force is many thousands of times weaker than ferromagnetic material they are also generally considered as ‘non-magnetic’.
MAGNETIC RAW MATERIALS
All the permanent magnets in the world are currently made from five types of material each with very different characteristics. The five types are alnico, ferrite, flexible rubber, and the rare earth magnets samarium cobalt, and neodymium. Read on to find out about each raw material, how the types of permanent magnets are made, and each one’s magnetic properties.
FERRITE (FE)
What is Ferrite?
Ferrite is a term used to refer to pure iron, the most easily recognisable ferromagnetic material. It is also a term used to describe ferrite magnetic material which is a compound consisting of strontium carbonate or barium and iron oxide (Fe2O3).
Ferrite magnets have low production costs but are also much weaker than rare earth samarium cobalt and neodymium magnets. Because of their low production costs they are one of the most widely used magnetic materials when high magnetic performance is not the most important factor.
Manufacturing
The method for producing ferrite magnets is not as costly or sophisticated as that for manufacturing rare earth magnets and because they are very hard and brittle they are generally manufactured in basic shapes such as squares, cylinders and rings.
The production of ferrite magnets begins with calcining a finely powdered mixture of iron oxide and strontium carbonate to produce a metallic-oxide material.
Once cooled, the already fine powder is then milled a number of times reducing the calcined material to fine particles smaller than 2 micrometres or 2 microns, so that each particle consists of one single magnetic domain.
The powder is then pressed and compacted into a die. If pressing takes place within an externally applied magnetic field the magnet's particles will be aligned and the magnet produced will be anisotropic. If the powder is pressed without an externally applied magnetic field the magnet will be isotropic and have weaker magnetic properties.
Once pressed, the compacted particles are then sintered at very high temperatures to make the particles fuse together before finally being magnetised.
Magnetic Properties
Ferrite magnets are inexpensive to produce which is relative to their overall magnetic strength. Despite being significantly weaker than rare earth materials they are still widely used in many commercial applications. The main strength of ferrite magnets is their resistance to demagnetisation and corrosion.
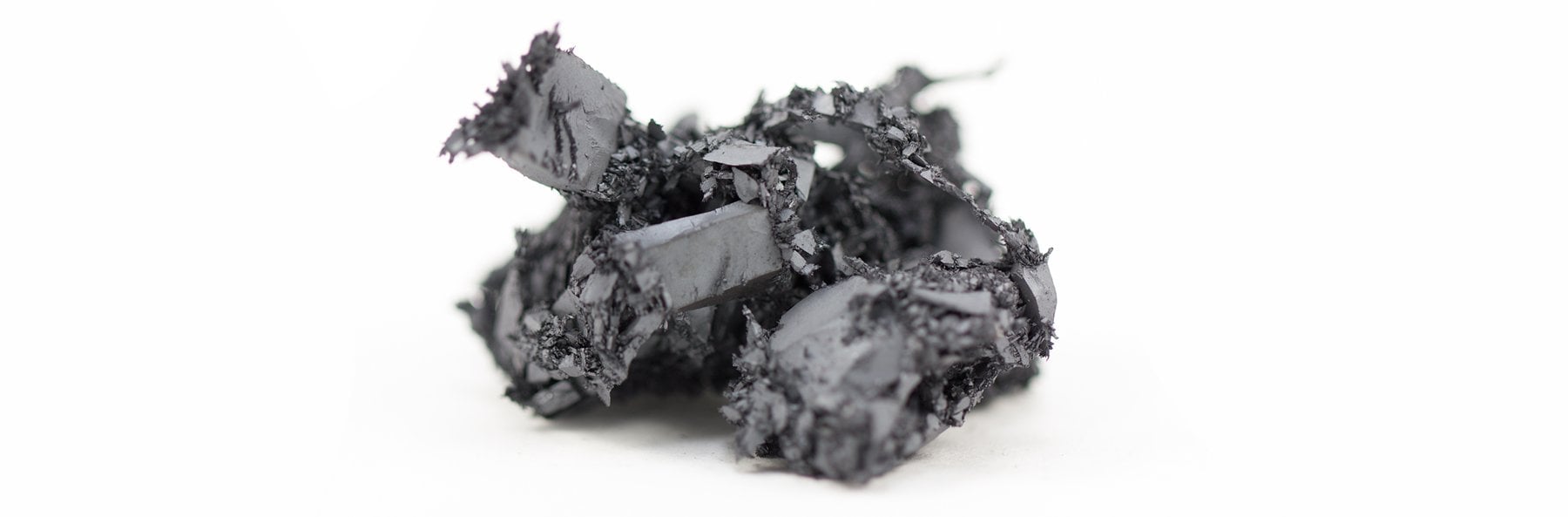
NEODYMIUM (NDFEB)
What is Neodymium?
Neodymium (Nd) is a rare earth element with the atomic number 60 that was discovered in 1885 by Austrian chemist Carl Auer von Welsbach. Although part of the rare earth family neodymium is relatively abundant and is no rarer than copper.
Neodymium is mixed with iron and boron as well as traces of other elements such as dysprosium and praseodymium to produce a ferromagnetic alloy known as Nd2Fe14b, the strongest magnetic material in the world. Developed in 1982 by General Motors and Sumitomo Special Metals, neodymium magnets have replaced other types of magnetic materials in many modern commercial and industrial appliances.
Manufacturing
Before neodymium can be made into neodymium magnets the mined rare earth mineral ore must be refined; a procedure involving dozens of chemical processes. Once refined, neodymium is mixed with iron, boron, and other required elements to make the desired grade by heating them in a vacuum induction furnace until melted. Generally, the molten alloy is then cooled to form ingots before being ground into tiny grains in a jet mill.
The super-fine powder is then pressed in a mould while simultaneously being exposed to a large magnetic field produced by an electromagnet. As the powdered material is pressed the magnetic field aligns the individual magnetic domains of the ferromagnetic material in the direction of the magnetic field. As the material is pressed the direction is set and the anisotropic material is given its preferred direction of magnetism.
This preferred direction of magnetism contributes to the finished magnets strength and high coercivity. If there is no external magnetic field applied during this stage of the process the material’s individual magnetic domains will not all be uniformly aligned (isotropic) and as result, the material can be magnetised in any direction.
However, the finished magnet will have a fraction of an anisotropic magnets strength and will have a lower coercivity.
Magnetic Properties
Neodymium magnets are the strongest magnets available and therefore have a high power to volume and weight ratio. Because they are so strong it also means they have a relatively low cost per unit of strength (Maximum Energy Product, MGOe). They have an incredibly high resistance to being demagnetised but generally have low maximum operating temperatures compared to other materials and are susceptible to corrosion if their coating is damaged.
Other grades of neodymium magnet, including special high maximum operating temperature grades are available. For more information regarding the properties of grades not mentioned above, please refer to our neodymium magnet grades page.

ALNICO (AL-NI-CO)
What is alnico?
The term alnico is an acronym of aluminium, nickel and cobalt; the three primary elements which are used to create alnico magnetic material. Despite being the first permanent magnets to be developed in the 1920s, rare earth magnets aside, alnico magnets are the strongest permanent magnets available. The introduction of alnico magnets meant that expensive electromagnets could be replaced with permanent magnets in devices such as motors, generators and loudspeakers.
Manufacturing
Alnico magnets have been manufactured for nearly 100 years and during this time the process has not drastically changed. The primary elements used to create alnico magnets are aluminium, nickel and cobalt, however, like other types of permanent magnets, traces of other elements are added to produce specific characteristics. Alnico magnets are manufactured using one of two methods:
Casting
Quantities of the individual elements used to manufacture alnico magnets are put into an induction furnace and melted. The molten material is then poured into a shell mould or larger green sand moulds. As the molten metal cools, the shell moulds start to burn and by the time the magnets are cold, the shell is almost disintegrated.
Patterns are similar in size to the required magnet size but with an additional allowance for shrinkage and machining to size. The magnet cavities inside are linked by runners which allow the molten metal to reach each magnet cavity and the runners are then scrapped and re-melted once the magnets are cast.
The newly cast magnets are then removed from the moulds before being fettled on grinding wheels to remove the runner gates. The magnets are then heated to incredibly high temperatures and then placed into magnetisers so that they can start to cool down whilst in the presence of a very strong magnetic field.
The magnets are then placed in large tempering ovens for a few days to temper and stabilise the magnets. The heat treatment stage of the process in conjunction with the alloy mixture gives the magnetic material its temperature handling characteristics and its final magnetic properties.
Finally, the magnets are inserted into a coil or solenoid magnetisers and in one-fifth of a second, the electrical pulse generates the necessary field needed to fully magnetise the magnets.
Sintering
Before sintered alnico magnets can be produced the raw elements must first be finely ground by milling into tiny particles. The powdered magnetic material is then pressed under tonnes of pressure in a die, which closely resembles the final desired shape.
Once the powder has been pressed, the material is sintered in a furnace in a hydrogen atmosphere at over 1200?. This process fuses all the pressed particles together to form one magnet.
The red hot material is then cooled in the presence of an external magnetic field to manufacture an anisotropic magnet or without an external magnetic field to produce an isotropic magnet. Generally, sintered alnico magnets do not require further shaping or machining as the die they are pressed in is made to be very close to the desired shape of the magnet. Finally, the raw magnetic material is magnetised by placing it inside a coil or solenoid magnetiser to magnetise the magnets.
Magnetic Properties
Alnico magnets are used in applications that require exceptional magnetic stability when operating at high temperatures as they lose less of their overall magnetic strength per increase in temperature than other permanent magnets.
They have the highest maximum operating temperatures of any permanent magnetic material, even up to 550 degrees celsius for some grades.
However, despite their resistance to high temperatures they are susceptible to demagnetisation, so much so that forcing two alnico magnets together in repulsion can permanently demagnetise both of them.

SAMARIUM COBALT
What is Samarium Cobalt?
Samarium cobalt (SmCo) is a magnetic material made of an alloy of the rare earth element samarium and hard metal cobalt as well as traces of iron, copper, hafnium, zirconium, and praseodymium. Like neodymium, samarium cobalt magnets are known as rare earth magnets as samarium is part of the same rare earth group of elements as neodymium.
Samarium cobalt magnets were developed in the early 1970s by the U.S. Air Force Materials Laboratory and were then the strongest magnets available until the introduction of neodymium magnets approximately ten years later. At the time of their introduction they were revolutionary, tripling the strength of the strongest available magnetic material.
Manufacturing
Samarium cobalt magnets are typically manufactured by a method of reduction and melting followed by a process of bonding or sintering the raw material to form the magnet. Sintering is the most common manufacturing method as described here.
Similarly to the process for manufacturing neodymium magnets the raw materials for producing samarium cobalt magnets are heated in an induction furnace and melted. The liquid alloy is then poured into moulds and cooled to form ingots. Once the ingots are cooled they are broken down and milled to produce tiny micron-sized particles of samarium cobalt powder.
The powder is then pressed using one of two methods; die pressing, where the powder is placed in a hard die and pressed or isostatic pressing where the powder is placed into a rubber die and pressed with equal pressure in all directions. Isostatic pressed magnets generally have better magnetic characteristics while die pressed magnets can be created to smaller dimensions.
Once the powder is pressed it is sintered at a temperature of up to 1250°C, fusing the powder into a solid. The sintered material is then given a solution treatment at similar temperatures before being tempered between 700°C and 900°C and then cooled in the presence of an externally applied magnetic field.
Finally, the magnetic material is machined, ground, and finished using water-cooled diamond-coated grinding machinery before being coated and magnetised.
Magnetic Properties
Samarium cobalt magnets are available in two types or grades, commonly referred to as series 1:5 and series 2:17. Both series’ have high magnetic strength and have maximum energy products up to 35MGOe.
Although they are not as strong as neodymium magnets their major strength is that they can maintain their performance in temperatures up to 350°C. They are also extremely resistant to corrosion, even without coating. However, because they contain cobalt, they are relatively expensive to produce.


FIND OUT MORE
Want to find out more? We have produced two sections of our site dedicated to rare earth magnets and to permanent magnets. Simply use the links below to continue reading.

RARE EARTH MAGNETS
Delve into the world of rare earth magnets. Explore the development of rare-earth magnets, the type of rare-earth magnets you can buy, and why they are so important to modern life.

PERMANENT MAGNETS
Discover more about permanent magnets including how to gauge the strength of a permanent magnet and the different ways permanent magnets can be magnetised.